Disk Chippers Vs Drum Chippers – what’s the difference between the two?
- Nathan Sangster
- Apr 21, 2024
- 3 min read
Updated: Jan 20
Commercial woodchippers are mostly made up of two versions – Disk chippers and Drum chippers. Disk chippers have been around longer, but these days drum chippers seem to be more common (in larger machines at least).
The cutter in a Disk chipper is exactly that – a large steel disk (20mm to 60mm thick) that spins with knives mounted to the face and machined slots behind the knives to let the cut timber through the disk and out the back. On the back of the disk large paddles are mounted and these use the centrifugal spinning action of the disk to throw the chips out of the cutting chamber, with very strong discharge force generated due to the larger diameter of the disk size. The timber is often fed into the disk on smaller machines at a 90° angle due to tight design space constraints, but on larger machines this infeed is angled at 30° or even 45° which makes the disk a lot more effective in cutting through larger diameter timber. The disk is also manufactured from a single solid piece of steel which if machined correctly and done with sound engineering principles, typically results in a very reliable and long-lasting cutter which will give thousands of hours of reliable service. On smaller machines with a 90° infeed, the infeed size opening is maximised for the disk to cut the timber against the anvil whereas as soon as the disk is angled to 30° or more, the infeed size ratio compared to the chipper disk size starts to be dramatically reduced and this is the greatest limiting factor of a disk chipper. It takes a larger disk size to get a respectable infeed opening size compared to a drum chipper design.
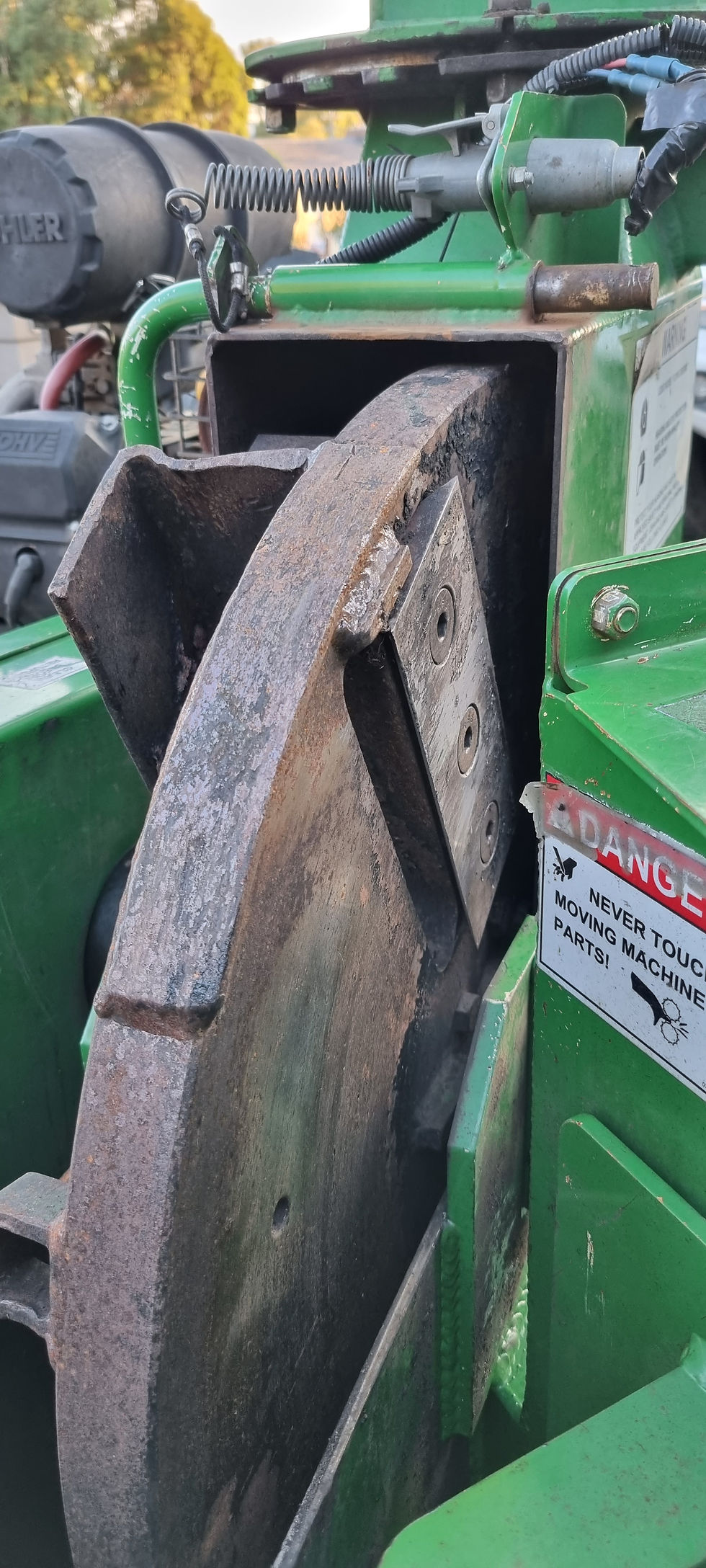
A drum chipper is also exactly that – a rotating drum with knives mounted on the drum face which cut the timber as it is fed into the cutting chamber. The knifes can’t simply just be mounted to the drum face though – to get the correct cutting geometry, the knives need to bolted to a set mounting block and right in front of that, a manufactured chip pocket which collects all of the chips as the knives are cutting the timber which are then thrown out of the pocket via centrifugal force up and out of the discharge chute. As a result, a chipper ‘drum’ is a highly complex manufactured work of art which if not manufactured correctly and to high precision tolerances, can quickly break down over time with the possibility that welds start to crack and as a worse-case scenario, catastrophic failure resulting from the drum flying apart.
So while the actual design of a drum chipper (as a manufactured part) is its potential weakness, the benefits are that a drum can be manufactured as wide as the designer wants relatively easily, meaning that a drum chipper can have a much larger infeed opening than a disk chipper equivalent which makes feeding difficult, crotchy material a lot easier. With the most efficient chipping action for a drum chipper being for the cutting action to happen in the lower half of the cutter arc, the larger the cutter drum then the more efficient the drum chipper will be.
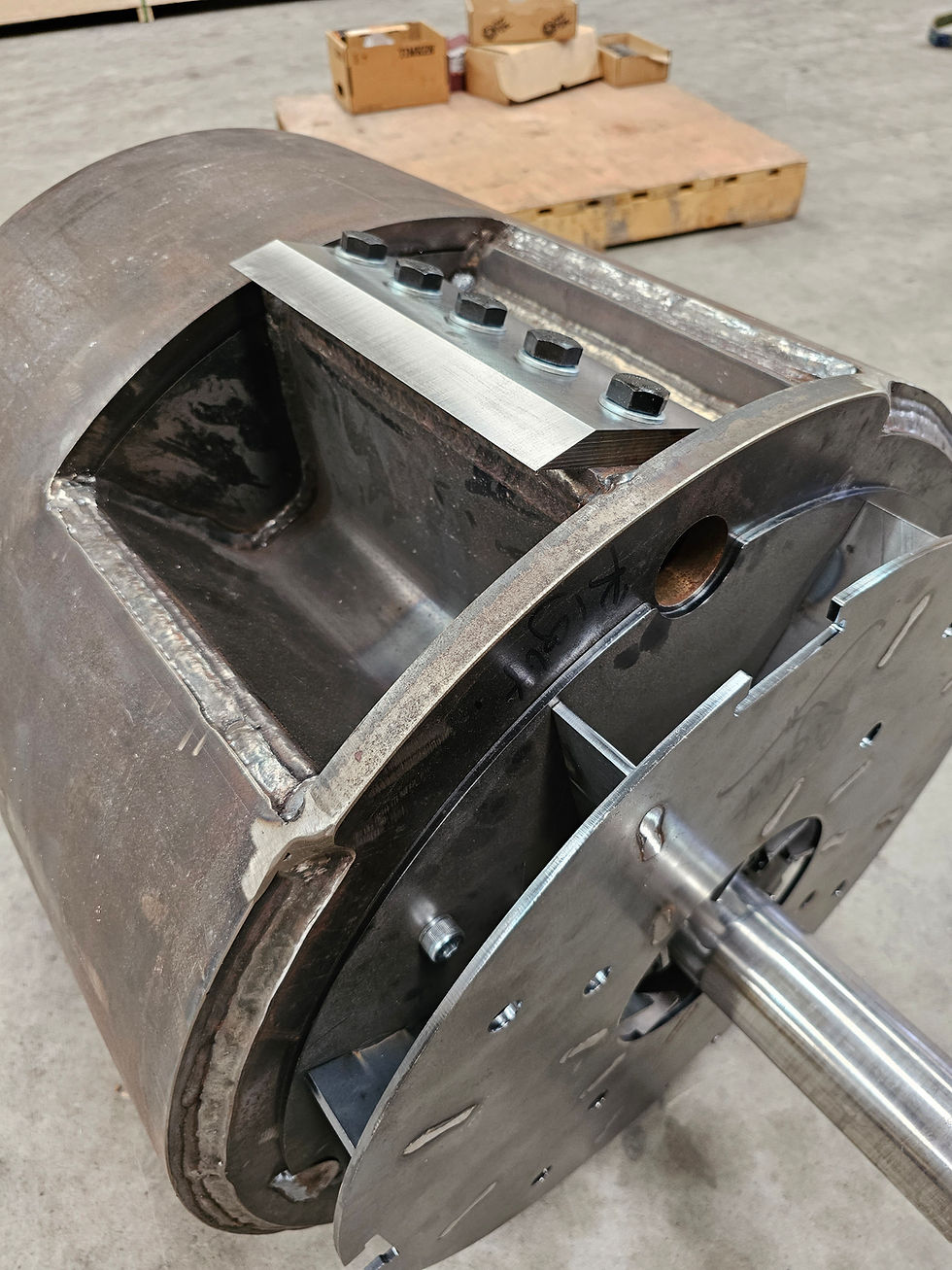
So what’s the verdict? With so many variables and differences in so many circumstances that wood chippers operate in, both styles of wood chippers are very much viable today and both perform extremely well in their own right so if you’re not sure what type or style of machine is best suited to your operation, then we recommend you speak with a seasoned professional that knows and understands the benefits and downfalls of both styles of machines to deliver the best solution to your particular need!
Comments